
Decoating service
Why decoating?
In the coating process, the coating is applied to almost everything in the coating chamber. The coating is desired on objects that are purposely placed in the equipment for the purpose of coating (tools, functional components, etc.). Coating is not desired on fixtures that are used to hold functional components and cover the coating chamber.
Coatings are applied to functional tools or components in order to increase their performance and service life. Many variables enter into the final quality of the coating, such as the preparation prior to the coating process, the number of layers previously applied on resharpened tools, the condition of the coating equipment, and the stability of the coating process. If there is a problem and the coating is poorly applied, it must be gently removed.
Decoating processes vary depending on the type of coating and the type of material being decoated. It is always necessary to choose a process that does not damage the material from which the tool was made. The reason for decoating is therefore to try to save them and clean the original surface before recoating with a functional coating.
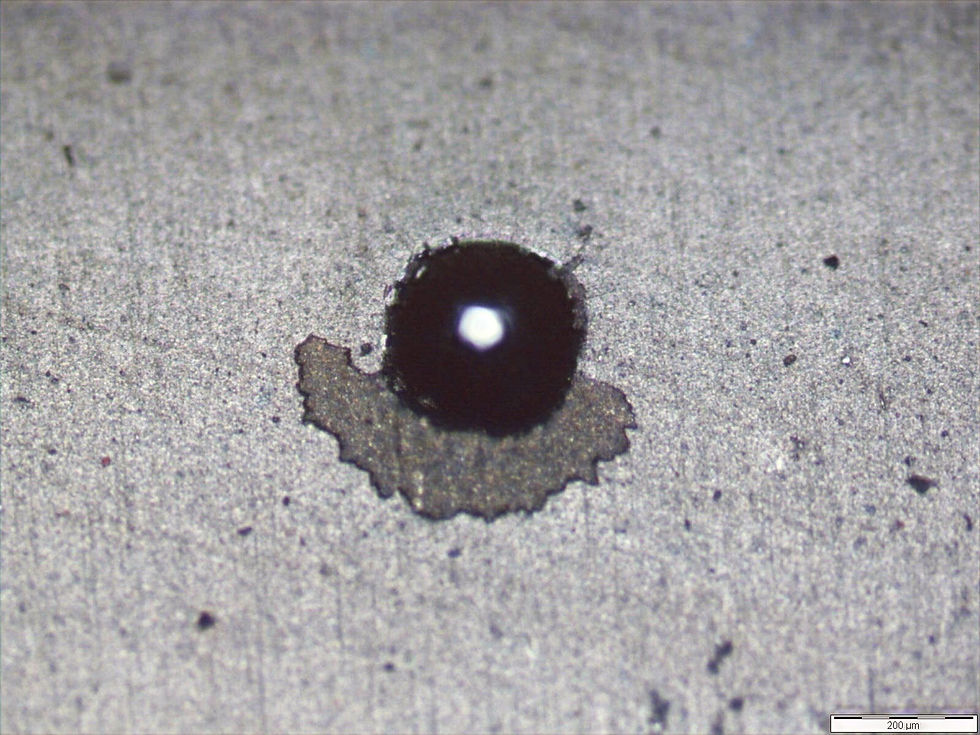


Šupiny odprýskutého povlaku mohou znečistit povrch povlakovaných předmětů
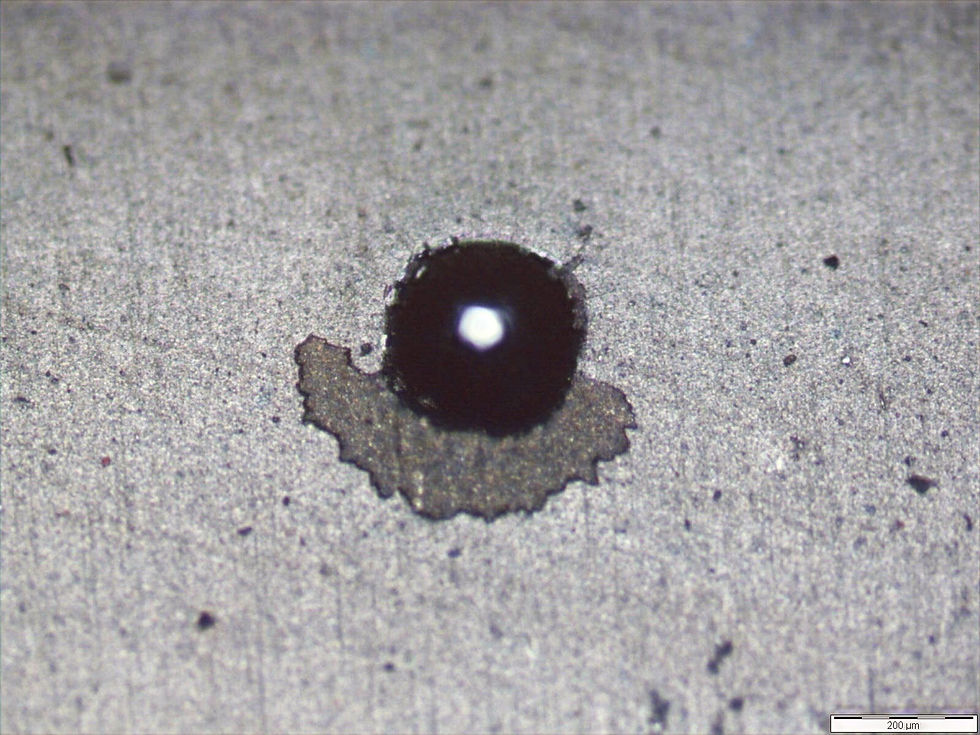
HM/HSS tool decoating
Poorly applied coating - Sometimes things just go wrong, either in the tool preparation before coating or during the coating process itself. If the tool or coating is unable to perform its function, it can be effectively removed with minimal impact on the substrate from which the tool was made. Tools after de-coating can look the same as before the coating process.
Tool refurbishment - The coating forms a durable protective barrier that protects the surface from external influences. Particularly for forming tools, the original coating should be well removed prior to actual surface refurbishment (welding, polishing).
Resharpened tools - Tools such as roll mills, taps, precision drilling tools, reamers or deep drilling tools should be decoated after resharpening and before recoating. This ensures higher precision and better surface quality of the machined hole. Particularly in deep drilling, the removal of previous coatings will result in a higher resistance to seizure and tool breakage.




Accessories for coating equipment
Unlike tools that are only in the coating chamber for one process, the various fixtures and fixing materials are exposed to dozens of processes. Each layer applied is characterized by a certain internal stress that compounds with the next layers applied until the coating peels off. The flaking pieces of coating can cause contamination of the surface of the coated parts, disturb the homogeneity of the coating at the cutting edge, contaminate the coating chamber and have a negative effect on the stability and speed of the coating process. In extreme cases, they may also pose a risk of injury to the operator of the coating equipment. Thick layers of coating can also have a negative effect on the smooth movement of various moving components in the coating machine.To remove PVD layers efficiently, our company uses mechanical and chemical methods, or a combination of both. We have designed and built our decoating systems as well as our own decoating procedures.
Individual and effective solutions for maximum customer satisfaction.
We offer our services for equipment and accessories from various coating equipment manufacturers such as CemeCon, Hauzer, Eifeler, Platit, Balzers and others.
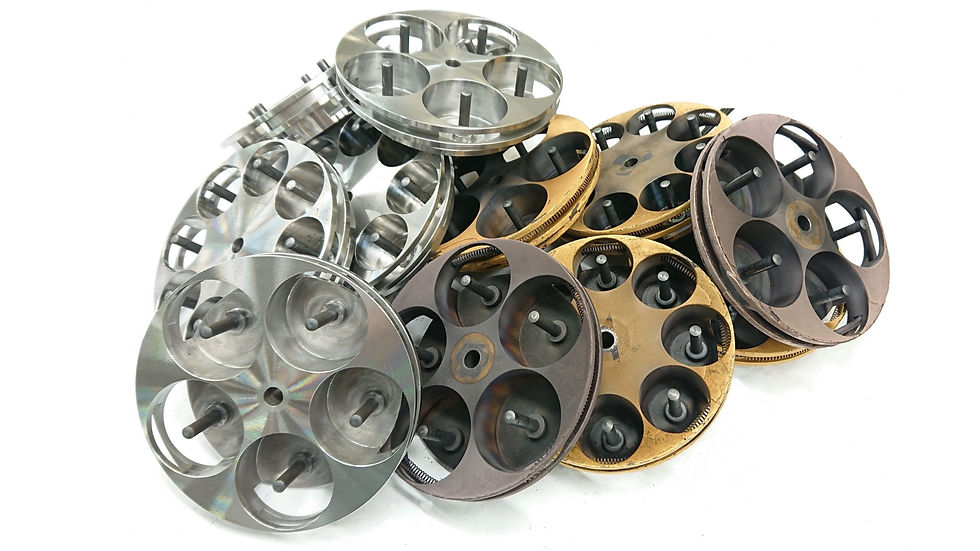


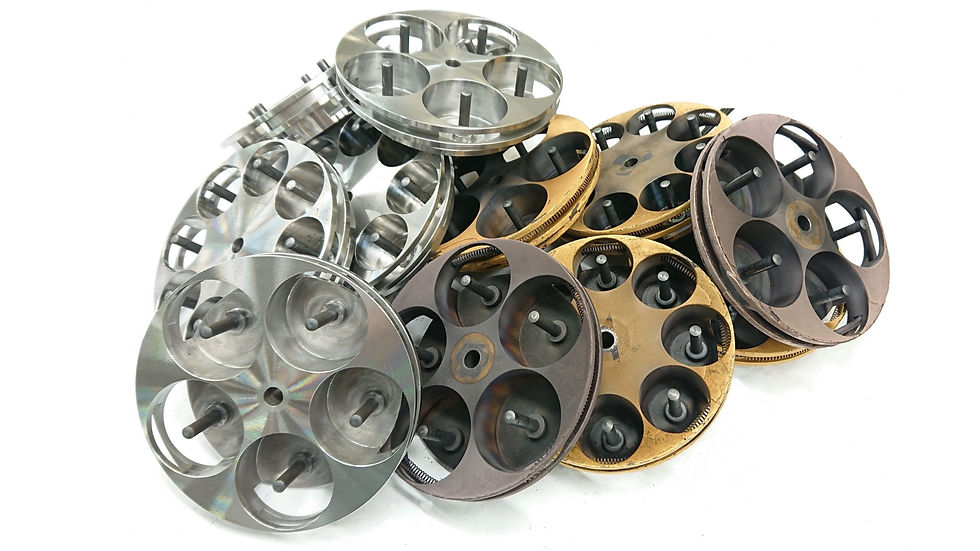
Component decoating
PVD coatings are not only applied to tools, but also to various components that have little to do with the cutting/forming process. These include various parts of internal combustion engines, gears, bearing segments, high-pressure pumps, etc. The applied coating acts as a barrier that has a protective, frictional or decorative function. Some coatings protect components from abrasion, some from corrosion, others reduce the need for lubrication and protect against seizure. Some coatings just look nice. But sometimes even such components need to be repaired and poorly applied coatings removed.
PVDeCoat Ltd. is able to remove all common Ti, Al, Cr based PVD coatings as well as DLC coatings from steel components without any substrate damage. The components retain their original shine and surface texture.
TiN, TiCN, TiAlN, TiSiN, AlTiN, TiAlSiN, TiAlCrN, TiB2, ZrN, AlCrN, CrN, DLC, Al2O3
- Coating removal without disturbing the substrate structure
- Appearance after decoating indistinguishable from a new tool


